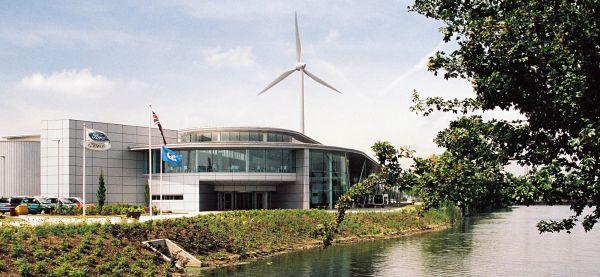
Este hecho ha sido posible al entrar en funcionamiento un tercer aerogenerador de ochenta metros de altura, con el que se ahorrarán 5.000 toneladas en emisiones de CO2 . El problema era que Ford iba a tener que usar más electricidad, ya que en breve comenzarían a producirse los nuevos TDCI 1.4 y 1.6, por lo que este tercer aerogenerador se hacía necesario para que la planta siguiera funcionando solo con la energía del viento.
Los dos generadores que Ford utilizaba en Dagenham rendían 5,92 millones de kWh al año, pero la sola incorporación de este tercero, que empezó a construirse en mayo, eleva la cifra a 11,4, gracias a sus 2,3 megawatios de cabacidad. Todos ellos son suministrados por la empresa Ecotricity.
Pero ésta no es la única planta que se sirve de la energía eólica para mantenerse operativa. La que Ford posee en Genk (Bélgica) también cuenta con dos aerogeneradores de dos megawatios y 150 metros de altura cada uno. En Genk se producen los Mondeo, Galaxy y S-Max. Todas las instalaciones de Ford se valen de algún tipo de energía renovable: La factoría de Niehl (Alemania) utiliza energía hidroeléctrica producida en Suiza y Noruega; en cambio, Bringfield, en Gran Bretaña, aprovecha la energía solar mediante paneles en su tejado -medida implantada también por Opel en Figueruelas-. El responsable de Ford en asuntos de sostenibilidad, Richard Douthwaite, explica: «Todas las fábricas tienen un diseño distinto y ofrecen diferentes oportunidades para adoptar energías verdes, con factores externos tales como condiciones del viento y horas de luz solar al día, por no hablar de las diferentes regulaciones locales».
Sin embargo, Ford no es ni mucho menos la única empresa automovilística pendiente de la eficiencia energética de sus fábricas. Una de las formas más comunes de reducir las emisiones de una factoría es el aprovechamiento de los residuos que la propia fábrica crea, para generar más energía. Es lo que hace Audi en su centro de diseño de motores en Neckarsulm (Alemania), al equipar el edificio con un sistema de aire acondicionado que no solo lo emite sino que recupera el calor disipado para obtener energía.
Una vez las grandes compañías han tomado cartas en el asunto con el proceso de fabricación, la asignatura pendiente que queda por investigar es el nivel de compuestos orgánicos volátiles (COV), entre los que se cuentan básicamente las pinturas disolventes. El ahorro de agua es otro campo en el que tienen trabajo por hacer, pues se gastan cantidades industriales -entre 2.000 y 3.000 litros por unidad, para pintarla, para los motores de las líneas de montaje, para climatización interior, etc-. Toyota va a la cabeza por lo que respecta a la reutilización de agua con su factoría de Valenciennes (Francia).