Estrecho de Magallanes, cerca de Punta Arenas, Chile. Hablamos del típico paraje azotado por el clima en el que ni los pingüinos quieren vivir y situado cerca de sitios míticos e inhóspitos como el pueblecito argentino de Ushuaia. Un lugar por el que sabemos que pasó el coche de Google Maps porque hay imágenes… pero del que no sabemos si consiguió regresar. Ahí, en Haru Oni, es donde Porsche ha decidido fabricar 550 millones de litros de gasolina sintética al año.
Haciendo honor a la verdad, hay que reconocer que Porsche es solo un socio del proyecto, y que participa con vistas, sobre todo, a tener acceso de primera mano a estos combustibles de nueva generación, de cara a poder poner a punto sus modelos para utilizarlos. Otros socios son Siemens, Man, Enel o Exxon Mobil (probablemente, esta última sea la más interesada en el resultado de la aventura).
Las cuestiones que nos debemos plantear es qué son los eFuels, cómo se van a fabricar en Haru Oni y qué repercusión pueden tener para el futuro de automóvil ‘convencional’, basado en un motor de combustión interna.
¿Qué es un eFuel?
Los eFuels (también conocidos como electrofuels, powerfuels, combustibles sintéticos basados en electricidad o combustibles renovables de origen no biológico) son hidrocarburos sintetizados a partir de hidrógeno (obtenido mediante agua y electricidad), y dióxido de carbono (procedente de aplicaciones industriales o capturado de la atmósfera).
Aunque no es obligatorio, la piedra angular de los eFuels es producirlos haciendo uso de fuentes de electricidad renovables (eólica o fotovoltaica) y, en particular, de excedentes de las mismas. De ahí el hecho de irse a las costas del Estrecho de Magallanes, cerca del Polo Sur; un sitio donde hay potentes vientos que están totalmente infrautilizados… y donde no existen habitantes o industrias capaces de darle un fin mejor a la electricidad eventualmente producida.
Al consumir CO2 durante su elaboración, los eFuels son una forma de descarbonización, y se les puede considerar una especie de sucesores de los biocombustibles de primera y segunda generación (los elaborados con granos como el maíz o desechos vegetales, respectivamente), ya que en su elaboración no interviene ninguna entidad biológica.
Son el equivalente a los lubricantes sintéticos, que son parecidos a los aceites minerales, pero están creados a partir de la nada. Y, al igual que ocurre con el lubricante sintético, los eFuels están naturalmente desprovistos de los residuos o impurezas asociados a los combustibles de origen fósil.
De esta manera, los eFuels carecen, por ejemplo, de restos de azufre, y su composición en cuanto a compuestos aromáticos (compuestos de carbono cuya molécula se cierra en forma de anillo) está muy controlada. Tienen el potencial para ser la mejor y más pura gasolina del mundo porque, en gran medida, están fabricados a medida para serlo
¿Cómo se va a fabricar eFuel en Haru Oni?
Lo primero que hay aclarar es que la planta de Haru Oni sólo es pionera en una cosa: en integrar en una misma instalación todo el proceso de elaboración de eFuels, desde la producción eólica a la sintetización del combustible. Sin embargo, las partes individuales del proceso son conocidas desde hace tiempo, y no resultan innovadoras en absoluto.
Sin embargo, precisamente por englobar toda la ‘cadena de valor’, Haru Oni es una buena maqueta a partir de la cual comprender cómo funciona la generación de eFuels. También va a ser un buen proyecto para averiguar exactamente cómo de baratos pueden llegar a resultar estos eFuels y dilucidar cuál debe ser su aplicación final más adecuada.
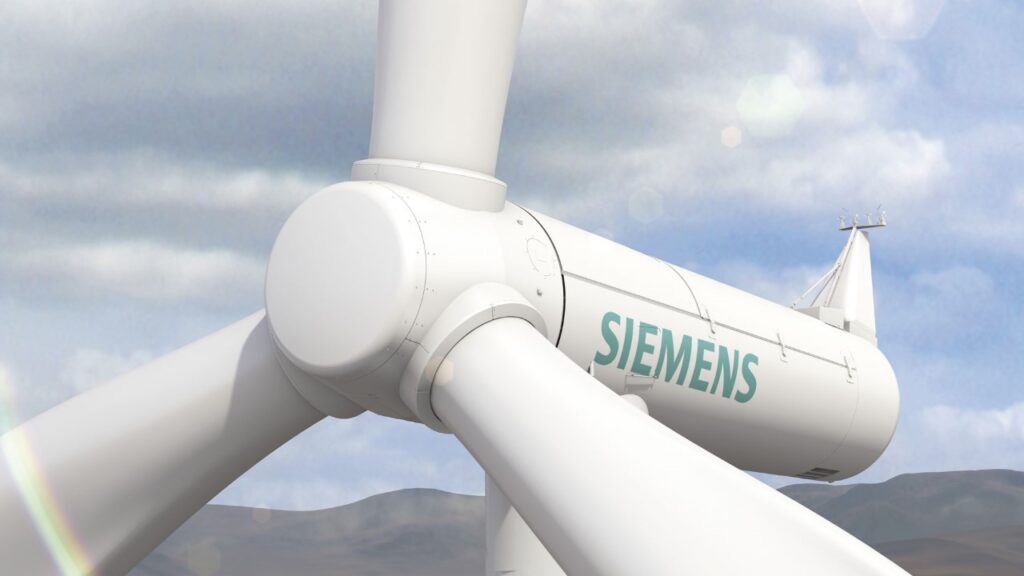
Para producir un eFuel, lo primero que necesitamos es una fuente de energía renovable. En el caso de Haru Oni, se va a emplear un molino eólico proporcionado por Siemens-Gamesa, de 3,4 MW de potencia, aunque la idea es llegar a instalar un pico de 2,5 GW de potencia en el año 2026. En Haru Oni hay viento fuerte y constante, de manera que es el lugar ideal para obtener energía eólica sin interrupciones. En esencia, lo que necesitas es una fuente de energía renovable que, aparentemente, esté absolutamente infrautilizada. Por ejemplo, podrías hacer lo mismo en África empleando placas solares (y de hecho, ya hay varios proyectos que contemplan hacerlo).
Después, esa energía eléctrica se emplea para abastecer todas las necesidades de la planta… que son muchas. Como en cualquier instalación industrial, hay mucho que bombear, comprimir, generar (especialmente, vapor de agua), refrigerar… etc. En cualquier caso, el uso clave de esa energía eléctrica es alimentar la parte de la planta encargada de, mediante electrólisis de agua cuidadosamente filtrada (por ejemplo, a partir de agua de mar y mediante ósmosis), producir hidrógeno.
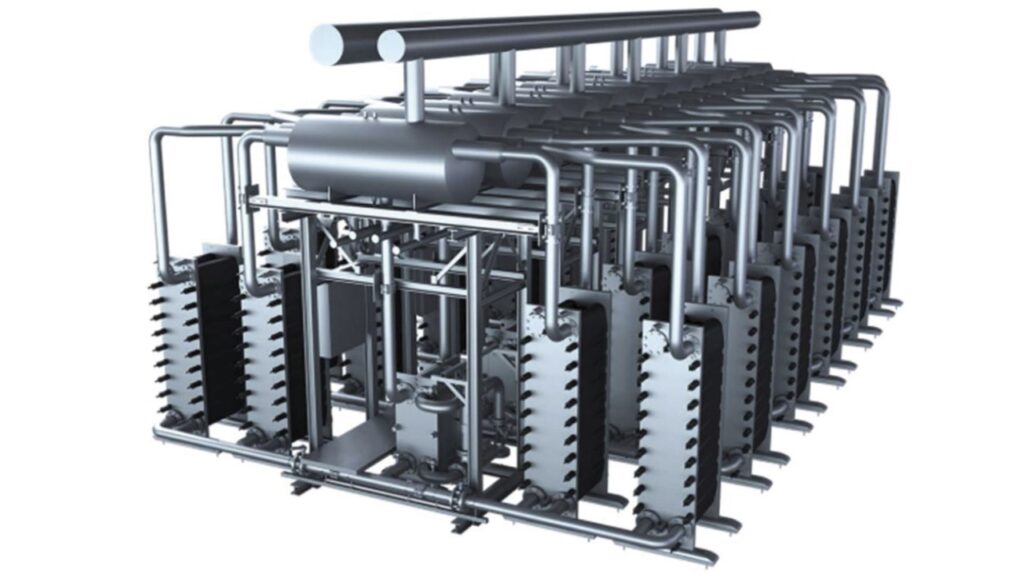
Los electrolizadores que se emplean para la generación de este hidrógeno trabajan de forma parecida a una pila de combustible ‘funcionando’ marcha atrás, y están basados en la misma tecnología de membrana de intercambio de protones o PEM que utilizan las pilas de combustible en automoción.
Estas membranas utilizan catalizadores como el platino, de manera que, aunque ofrecen eficiencias de hasta el 70%, resultan caras de fabricar. En concreto, Haru Oni está empezando a trabajar con un Siemens Silycer como el de la fotografía, capaz de producir 20 kilos de hidrógeno por hora con un consumo eléctrico de 1,25 MW y una eficiencia del 65%.
Obviamente, la idea es ampliar cuanto antes la instalación original, añadiendo aerogeneradores y electrolizadores, pero manteniendo siempre esa relación aproximada 2:1. Es decir, la planta de electrólisis va a consumir alrededor del 50% de la energía renovable que generen los molinos, y esa energía se va a invertir en producir hidrógeno.
A la salida del electrolizador, obtenemos dos caudales separados. Por un lado, tenemos agua pura con una buena cantidad de oxígeno disuelto. Y por otro lado, tenemos hidrógeno ‘verde’. Ahora, podríamos convertir ese hidrógeno en un producto más transportable (como, por ejemplo, amoníaco, a través de un proceso Haber-Bosch)… pero no estaríamos cumpliendo ninguno de nuestros dos objetivos; no estaríamos retirando CO2 de la atmósfera ni estaríamos acabando con una sustancia capaz de alimentar un motor de combustión interna.
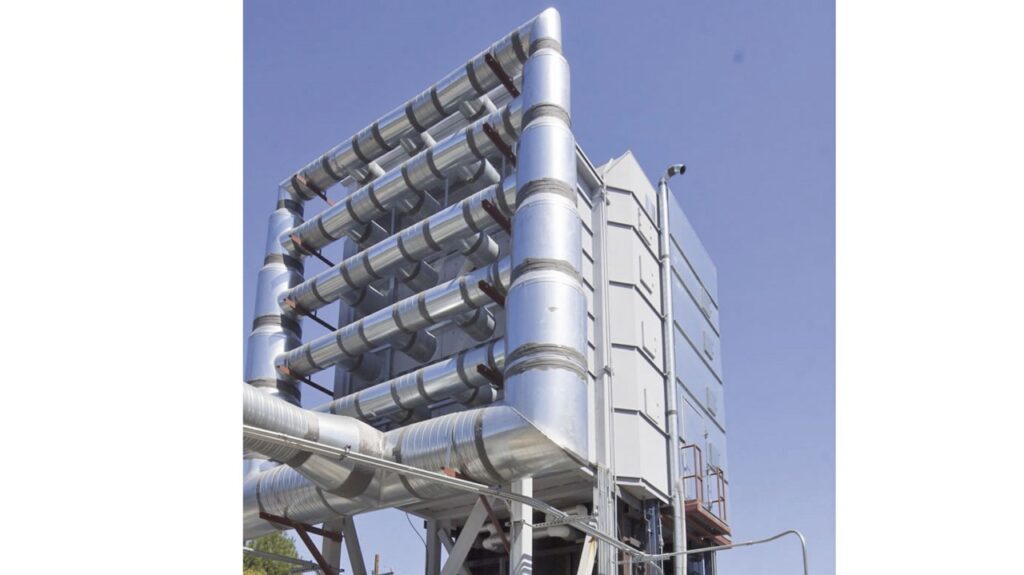
El siguiente paso consiste en secuestrar CO2 de la atmósfera. Aproximadamente el 0,3% del aire que respiramos es CO2… y la idea de todos estos esfuerzos es evitar que esa cifra llegue al 0,4% y combatir así el efecto invernadero.
La única forma rentable (en términos energéticos) de extraer CO2 de la atmósfera es utilizar sustancias en las que se disuelva muy bien, como por ejemplo soluciones alcalinas (el hidróxido cálcico es un buen ejemplo). De manera que montamos una torre de absorción por la que se hace pasar el aire, y el compuesto elegido funciona como una especie de esponja de dióxido de carbono. En el caso de Haru Oni, se utiliza una torre de extracción fabricada por Global Thermostasts, y que utiliza unos bloques parecidos a catalizadores de coche, embebidos en un compuesto basado en una amina (grupos de tipo NH2).
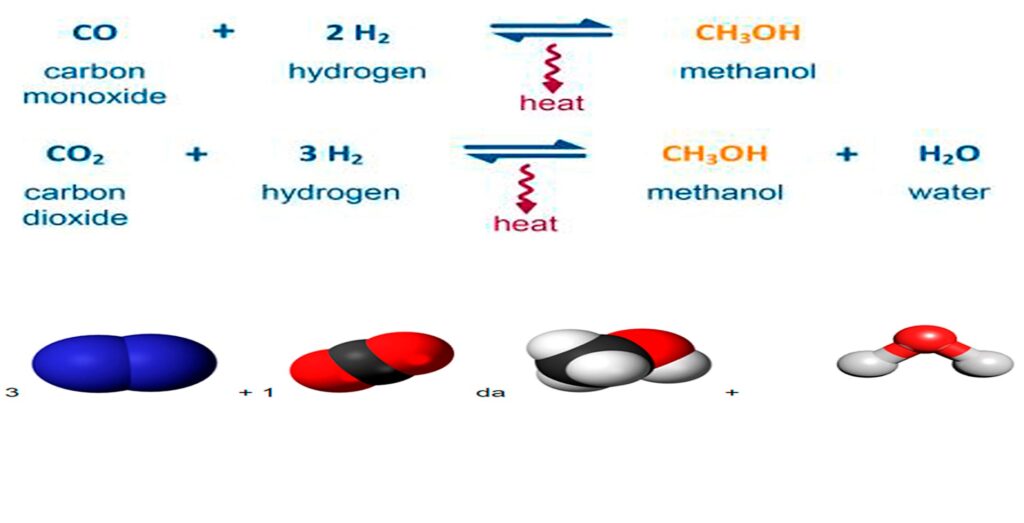
Una vez que tenemos hidrógeno y dióxido de carbono, llega el momento de hacerlos reaccionar para obtener nuestra primera sustancia combustible. Ambos gases se mezclan en las proporciones adecuadas y, bajo la actuación de un catalizador, se combinan para dar metanol (el tipo de alcohol más básico, de fórmula CH3OH), agua, y un montón de calor que se extrae mediante un sistema de refrigeración y se reutiliza, por ejemplo, para generar el vapor que se emplean en las torres de absorción de CO2. En Haru Oni, el metanol se produce en unas torres de reacción (denominadas convertidores) fabricadas por MAN Energy Services.
El rendimiento de este proceso no es muy bueno, de manera que tras cada pasada, se recupera por condensación el metanol producido, y la mezcla de hidrógeno y dióxido de carbono se vuelve a pasar. Al final de esta fase tenemos, por fín, una sustancia combustible que es líquida a temperatura ambiente. No obstante, aún estamos a un paso de tener gasolina.
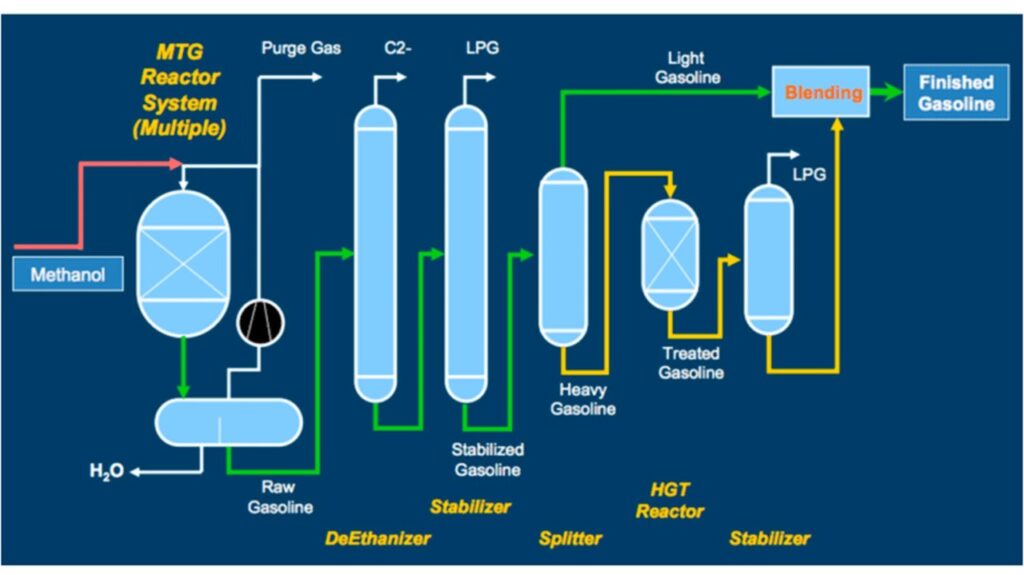
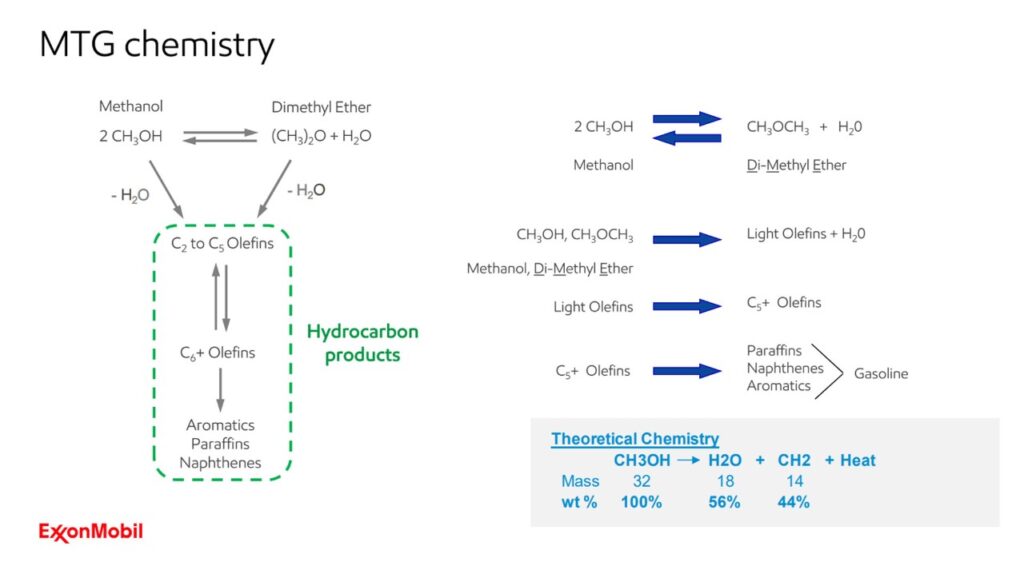
La última fase del proceso es el reactor MTG, del inglés methanol-to-gasoline. El reactor MTG de Haru Oni lo fabrica Exxon Mobil. Este reactor se alimenta con metanol casi puro, que progresivamente se va convirtiendo en compuestos orgánicos con mayor número de carbonos, hasta llegar a cadenas de aproximadamente 11 carbonos, que es una composición muy parecida a la gasolina ‘natural’.
El proceso, sin embargo, y tal como puedes ver en el gráfico superior, no es en absoluto un camino de rosas, y se generan muchos compuestos ‘colaterales’ que hay que ir retirando. Se trata de compuestos ligeros, como el etano, el propano o el butano, y otros más densos y exóticos (como el dureno), que componen lo que denominamos ‘gasolina pesada’, y que hay que reprocesar para ‘simplificarlos’. En cualquier caso, se trata de un proceso que Exxon Mobil lleva poniendo a punto desde 1970 y que actualmente se puede considerar industrialmente maduro.
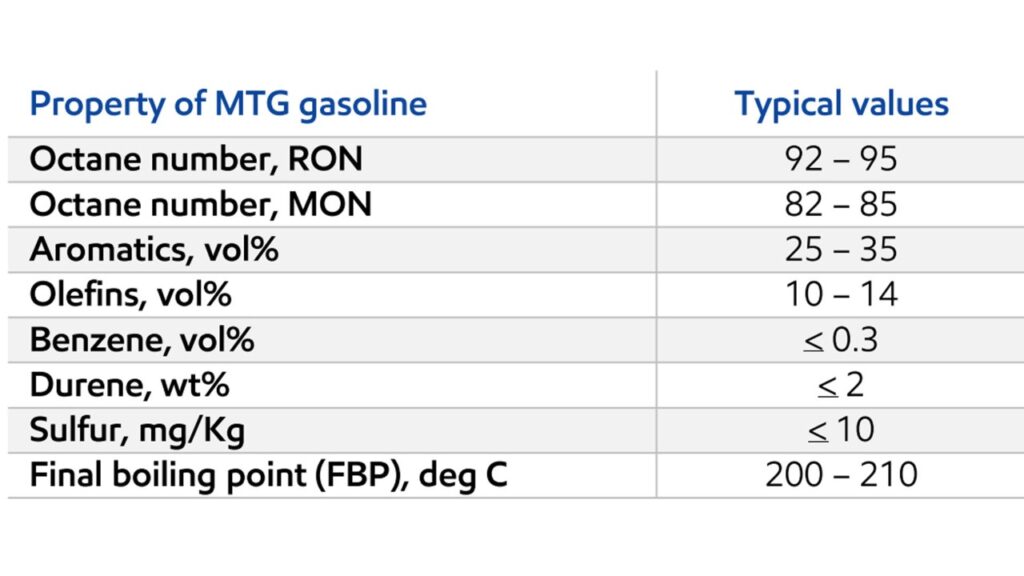
Esta gasolina sintética no tiene exactamente las propiedades de la gasolina natural y, aunque debería funcionar sin problemas, es uno de los aspectos que Porsche quiere comprobar: si da problemas a corto, medio y largo plazo. Es decir, si se puede homologar para utilizarla en algunos o todos sus coches ya vendidos… o si tiene que introducir modificaciones para hacer que sus futuros modelos sean compatibles con este tipo de combustibles sintéticos.
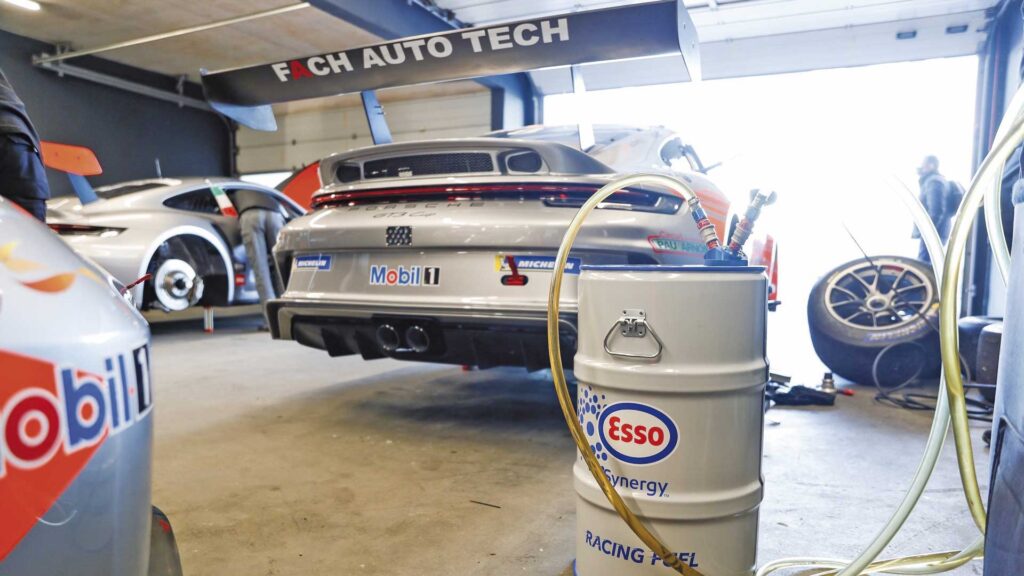
Actualmente, Porsche ya está realizando experimentos con combustibles de procedencia alternativa, en colaboración con Exxon Mobil. Por ejemplo, todo el combustible que se use en las temporadas 2021 y 2022 de la Porsche Mobil1 Supercup va a consistir en Esso Renewable Racing Fuel, una mezcla de gasolina y biocombustibles de segunda generación (obtenidos a partir de la fermentación de restos vegetales no aprovechables). La idea de Porsche es dar el salto al eFuel en la temporada 2023, con combustible procedente de Haru Oni.
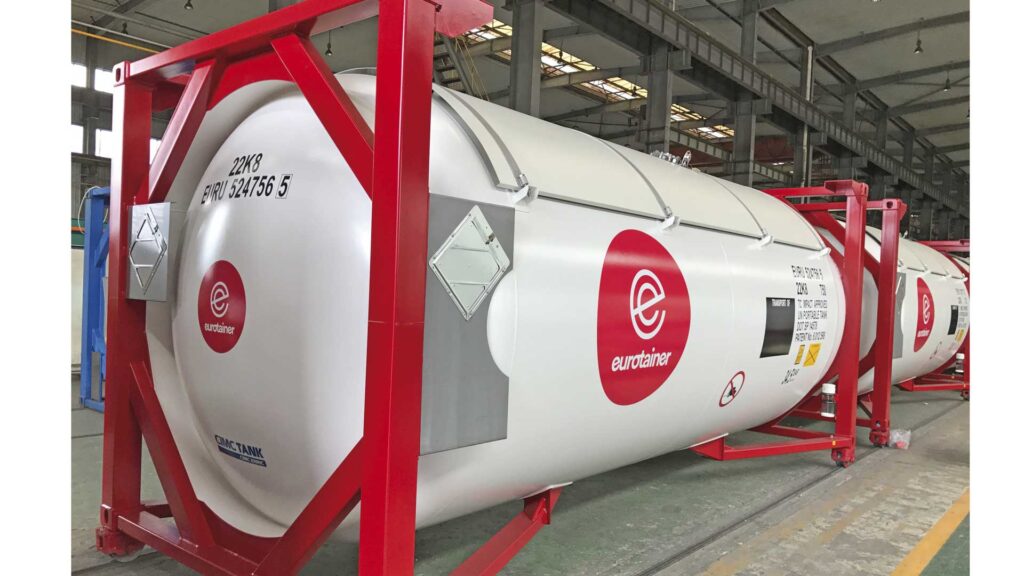
El paso final es envasar la gasolina producida en depósitos de 30.000 litros y llevarla en barco hasta Europa, donde puede empezar a ser consumida. Esta gasolina es relativamente ‘neutra en carbono’, ya que se ha producido secuestrando de la atmósfera aproximadamente el mismo CO2 que va a liberar durante su combustión.
Es cierto que esl CO2 no se libera exactamente donde se secuestró (de hecho, se libera en la otra punta del mundo), pero eso no es un problema en términos medioambientales: el CO2 es un gas que contribuye al efecto invernadero pero, a diferencia de compuestos tóxicos como el monóxido de carbono o los óxidos de nitrógeno, no afecta a la calidad local del aire (por ejemplo, en las ciudades).
Por supuesto, la neutralidad total es imposible. Hay que tener en cuenta que todos los pasos que hemos visto introducen ineficiencias más o menos grandes, de manera que el producto final, además de caro (comparado con el proceso habitual de hacer un agujero en el suelo y robarle los ahorros a la Madre Naturaleza en forma de petróleo), tiene asociada cierta ‘intensidad de carbono’. Demonios… el mero hecho de llevar esta gasolina desde Chile y hasta Europa en un barco mercante no puede considerarse un proceso especialmente limpio.
[sf_btn type=»newsletter» txt=»¿Quieres recibir nuestra newsletter? Haz clic aquí» url=»https://www3.actito.com/wf/200262/52/es/Start.act»]